کنده های چوب که مواد اولیه برای تولید تخته سه لا هستند تحت پردازش هیدروترمال قرار می گیرند. پردازش هیدروترمال در استخرهای خیساندن پر از آب در دمای 40 تا 60 درجه سانتی گراد بسته به گونه چوب انجام می شود. در مرحله بعد، از طریق پوستزدایی مکانیکی، کندهها از پوست و بقایای مواد معدنی انباشته شده در پوست در طول فرآیند برداشت و حمل و نقل پاک میشوند.
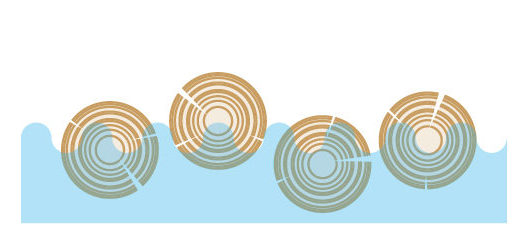
2. لایه برداری
یک کنده چوب بریده شده به اندازه به یک دستگاه لایه برداری چرخشی تحویل داده می شود. هنگامی که در یک دستگاه تراش دوار در زاویه ای راست قرار می گیرد، یک کنده در برابر تیغه می چرخد. تیغه لایه بردار لایه ای از روکش را به شکل نوار روکش برش می دهد.
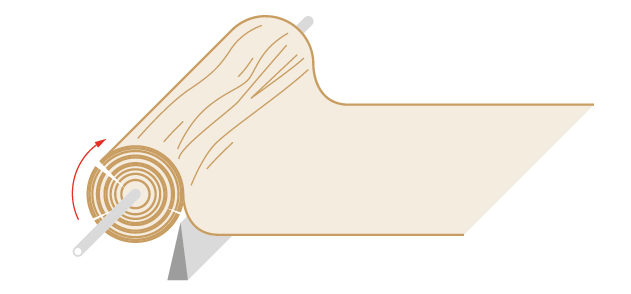
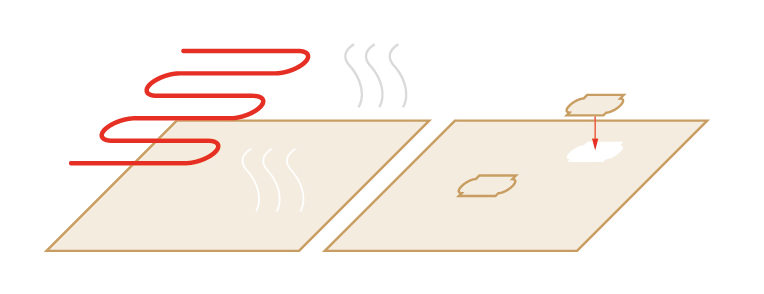
3. خشک کردن و ترمیم سطح روکش ها
در این مرحله ونیرها دارای رطوبت 30-120٪ هستند. به منظور کاهش رطوبت تا حد مورد نیاز، روکش ها در یک فرآیند مستمر در تاسیسات خشک کردن نواری یا به صورت ورق در تاسیسات خشک کن غلتکی، در دمای 160 تا 180 درجه سانتی گراد خشک می شوند تا به رطوبت مورد نظر در حدود 8 برسند. – 12 درصد هر گونه نقص روکش ناشی از آناتومی چوب (به عنوان مثال گره ها، لرزش های بسته، آثار جوانه ها و غیره) با استفاده از سیستم های اسکن تخصصی شناسایی می شوند. چنین عیوب سطحی با درجهای روکش یا قلابهایی که از نظر رنگ و الگوی چوبی مطابقت دارند، ترمیم میشوند.
4. کاربرد چسب و مونتاژ مجموعه تخته سه لا
مجموعه روکش های صورت و هسته با انتخاب و چیدمان ورق های روکش به روشی مناسب مونتاژ می شوند. بسته به کاربرد مورد نظر محصول نهایی و نیاز مشتری، ورق ها به صورت کلاسیک به صورت دانه بندی متقاطع، دانه بندی متقاطع و موازی و یا دانه بندی موازی نسبت به یکدیگر قرار می گیرند. چسب از هر دو طرف روی هر ورق دوم روکش اعمال می شود. نوع ترکیب چسب، نوع اتصال مورد استفاده برای تخته چندلای خاص را تعیین می کند.
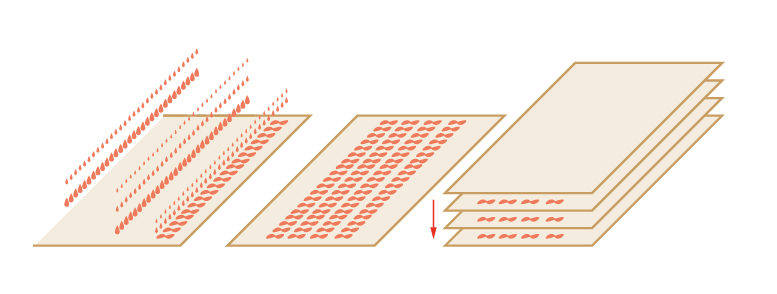
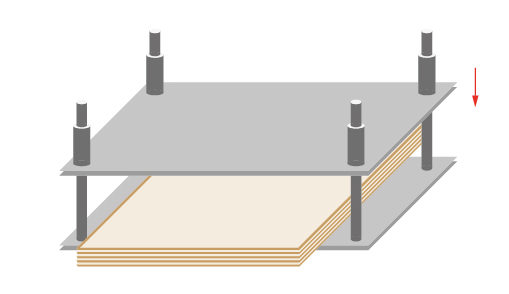
5. پرس داغ
مجموعه روکش ها در پرس های هیدرولیک چند صفحه ای تحت فشار تحت فشار گرم قرار می گیرند. روکش ها به هم فشرده می شوند و از این پس به طور دائم به هم می چسبند.
6. پردازش و سنباده نهایی
پس از چاشنی سازی تخته سه لا، ورق های تخته سه لا در نهایت پردازش شده و با برش مواد اضافی بر روی دستگاه پروفیل به اندازه مورد نظر بریده می شوند. سپس سطوح روکش های صورت در یک دستگاه سنباده دقیق کالیبره و سنباده می شوند.
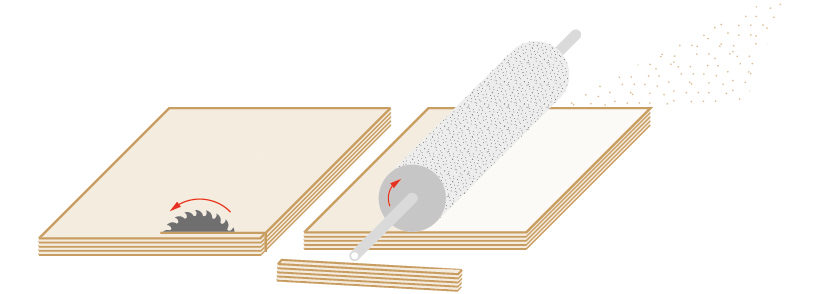
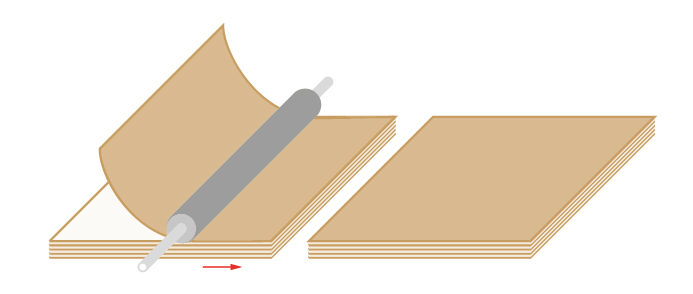
7. پوشش، فیلمبرداری، درمان سطح
در صورت نیاز به کاربرد نهایی پانل تخته سه لا، در این مرحله از فرآیند، یک کاغذ مخصوص آغشته به رزین (که به عنوان فیلم نیز نامیده می شود) روی سطح تخته چندلا اعمال می شود. این فرآیند در محیط با فشار و دمای بالا انجام می شود و باعث می شود رزین به روکش های هسته عبور کند و در نتیجه سطحی با ویژگی های عملکردی جدید تولید کند.
8. بازرسی کیفیت و مرتب سازی درجه
دسته بندی تخته چندلا بر اساس بازرسی کیفی و طبقه بندی روکش های روکش تخته سه لا مطابق با الزامات سیستم های کیفی، استانداردهای فنی و مشخصات می باشد.
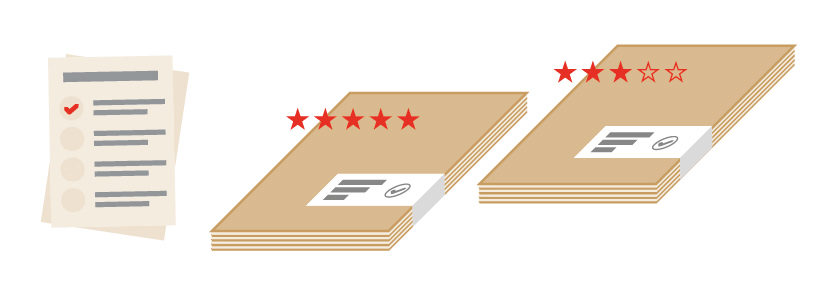
تخته چندلا یک محصول پانل بر پایه چوب است که از مجموعه ای از روکش ها تشکیل شده است که با یک رزین به هم چسبانده شده اند. برای جمع بندی فرآیند تولید؛ کنده ها به صورت روکش پوست کنده می شوند، روکش ها را با چسب کف می کنند، طوری چیده می شوند که جهت دانه بندی هر روکش عمود بر روکش مجاور آن باشد، به هم فشرده شده، بریده شده و سنباده می شود.
اما در فرآیند تولید چیزهای بیشتری از این وجود دارد…
مرحله 1: جنگل
برای ما مهم است که تمام کنده های خام مورد استفاده در تخته سه لا از امتیازات قانونی و پایدار جنگل تهیه شده باشند. ما فقط از کارخانه هایی استفاده می کنیم که از سیاست خرید مسئولانه فدراسیون تجارت چوب برای اطمینان از این امر استفاده می کنند.
هنگامی که درختان به سطح قابل قبولی از بلوغ رسیدند، توسط دروگرهای آموزش دیده قطع می شوند. بسته به عملکرد آسیاب می توان از وسایل نقلیه ای مانند آنچه در تصویر بالا است برای انتخاب و قطع درختان با استفاده از تصاویر ماهواره ای استفاده کرد.
مرحله 2: حمل و نقل به آسیاب
کنده ها از امتیاز جنگل به آسیاب منتقل می شوند تا پردازش شوند.
حمل و نقل در برخی موارد مشکلات زیست محیطی خاص خود را دارد، زیرا مناطق جنگلی برای ایجاد فضایی برای جاده ها پاکسازی می شوند و بنابراین درختان جدید نمی توانند رشد کنند.
مرحله 3: حوضچه چوب
به محض ورود به آسیاب، کنده ها در محوطه چوب ذخیره می شوند. آسیاب ها از روش های مختلفی برای حفظ رطوبت در کنده ها استفاده می کنند، بسیاری از آنها سیستم های اسپرینکلر را انتخاب می کنند. لاگها در نهایت به Log Pond میرسند. کنده ها برای مدت طولانی در آب غوطه ور می شوند تا به اندازه آنها بریده شود و راحت تر پوست کنده شوند. برخی از آسیاب ها در آب و هوای سردتر، حوضچه های چوبی گرم دارند، زیرا گرما نیز کیفیت لایه برداری را بهبود می بخشد. آنها از این به عنوان پردازش هیدروترمال یاد می کنند.
مرحله 4: پوست کندن سیاههها
قبل از برش و پوست کندن کنده ها، پوست باید جدا شود. آسیاب ها از ماشین آلات صنعتی مانند این برای جدا کردن پوست درختان در طول خط تولید استفاده می کنند.
مرحله 5: برش سیاهه ها
کنده های پوست کنده شده، سپس به اندازه هایشان بریده می شوند. اندازه ای که کنده ها به آن بریده می شوند معمولاً به تولید در زمان برش بستگی دارد. اندازه پانل تمام شده و جهت دانه در برش کنده ها نقش دارند.
مرحله 6: کندن کنده ها
کنده ها با استفاده از تراش چرخشی پوست کنده می شوند. این کار کنده را به روشی شبیه به مداد تراش کنده می کند به جز اینکه تیغه در زمان برش کاملاً موازی با کنده است. شما میتوانید این فرآیند را در ویدیوی بالا مشاهده کنید و در ویدیو زیر مشاهده کنید که آنها از پشت دستگاه لایهبردار مستقیماً روی نوار نقاله بیرون میآیند.
مرحله 7: اندازه و درجه بندی
پس از پوست کندن ورق های حاصل، مانند تصویر زیر به مرحله بعدی روی نوار نقاله هدایت می شوند.
پس از لایه برداری، روکش ها در طول خط تولید در جریان های طولانی منتقل می شوند. آنها باید به اندازه بریده شوند و مراحل درجه بندی اولیه را طی کنند. درجه بندی در مورد تخته چندلای توس بسیار مهم است، بنابراین اکثر کارخانه ها از فناوری اسکن برای بررسی نقص در روکش ها، برش به اندازه های مورد نیاز و سپس جداسازی روکش های بالقوه صورت از روکش های اصلی استفاده می کنند.
برخلاف آسیابهای اروپای شرقی و بالتیک، کشورهایی مانند چین روکشها را در مربعهای کوچکتر پوست میکنند و سپس به عنوان روشی مقرونبهصرفه (اما کاهش کیفیت) آنها را به اندازه مناسب بخیه میزنند.
مرحله 8: خشک کردن روکش ها
در این مرحله، روکش ها به دلیل خیساندن در حوضچه چوبی هنوز خیس هستند. روکش ها به دلایل مختلفی باید خشک شوند. از محافظت از چوب در برابر پوسیدگی قارچی تا افزایش خواص مکانیکی تخته تمام شده. اکثر کارخانه ها از خشک کن های صنعتی و بزرگ استفاده می کنند که اغلب از طریق تسمه نقاله به لایه بردار متصل می شوند. با این حال می توان از روش های مقرون به صرفه تری نیز استفاده کرد. به عنوان مثال، برخی از لایه بردارها در چین، روکش ها را در فضای باز می گذارند تا در طول روز خشک شوند.
مرحله 9: تعمیر عیوب
پس از خشک شدن، روکش ها باید در جایی که نقص وجود دارد، تعمیر شوند. به عنوان مثال در مورد تخته چندلای توس، گره های باز (جایی که شاخه ها قبلاً وجود داشتند) را می توان “وصل کرد”. شکاف های روکش روی تخته سه لا را نیز می توان پر کرد و روکش های با اندازه نامناسب را می توان با انگشت به هم متصل کرد (به بالا مراجعه کنید). . برخی از آسیاب ها دارای دستگاهی هستند که روکش ها را اسکن می کند و به طور خودکار سوراخ ها یا گره های باز را مسدود می کند. (پایین را ببینید).
مرحله 10: استفاده از چسب و لای آپ
روکش ها از طریق یک دستگاه چسب اجرا می شوند که اساساً چسب را روی صورت و پشت روکش می چرخاند. سپس آنها را روی یک روکش بدون چسب قرار می دهند تا پشته متناوب شود. چسبیده، بدون چسب، چسب، بدون چسب و غیره.
مرحله 11: پرس سرد
پرس سرد پس از استفاده از چسب به منظور آماده سازی روکش ها برای پرس گرم اتفاق می افتد. این کار باعث صاف شدن روکش ها می شود و اطمینان حاصل می کند که چسب به طور یکنواخت در سراسر روکش ها پخش می شود.
مرحله 12: فشار دادن داغ (پرس نور روز)
این بخش از فرآیند تولید جایی است که پانل های واقعی شروع به شکل گیری می کنند. پانل های متعدد در مطبوعات نور روز بارگذاری می شوند. سپس پرس دی لایت فشار گرم را برای مدت طولانی روی تخته ها فشرده و حفظ می کند. این باعث ایجاد و حفظ تماس مورد نیاز بین چسب و روکش می شود. همچنین کشش در خط چسب و ضخامت لایه چسب را کاهش می دهد.
مرحله 13: پیرایش، سنباده زدن و تکمیل
پس از پرس داغ، تخته قبل از پردازش بیشتر برای تثبیت و خنک شدن باقی می ماند. سپس می توان هر روکش اضافی را کوتاه کرد تا تخته دارای لبه های مربعی باشد، سپس تخته ها معمولاً با استفاده از یک سنباده صنعتی بزرگ سمباده می شوند.
مرحله 14: کنترل کیفیت
محصول نهایی باید از نظر کیفیت مورد ارزیابی قرار گیرد، اما صرفاً منتظر ماندن تا پایان فرآیند برای یافتن یک مشکل بزرگ در تولید، بسیار کارآمد نخواهد بود. به همین دلیل، آسیاب ها با انجام تعدادی آزمایش بر روی بخش های مختلف فرآیند تولید، مانند آزمایش سطوح رطوبت، آزادسازی فرمالدئید، دوام و غیره، تولید خود را کنترل می کنند.
بسیاری از کارخانه ها دارای گواهینامه کنترل تولید کارخانه هستند که به این معنی است که توسط شخص ثالث ممیزی شده و فرآیند تولید آنها مطابق با استانداردهای اروپایی تایید شده است.
مرحله 15: بسته بندی
سپس محصولات تمام شده روی هم چیده شده و به هم متصل می شوند. هر گونه علامت CE مربوطه روی بسته بندی چاپ می شود.
I am really inspired together with your writing skills as neatly as with the structure on your blog. Is this a paid subject or did you customize it yourself? Anyway keep up the excellent quality writing, it’s uncommon to peer a great blog like this one these days!